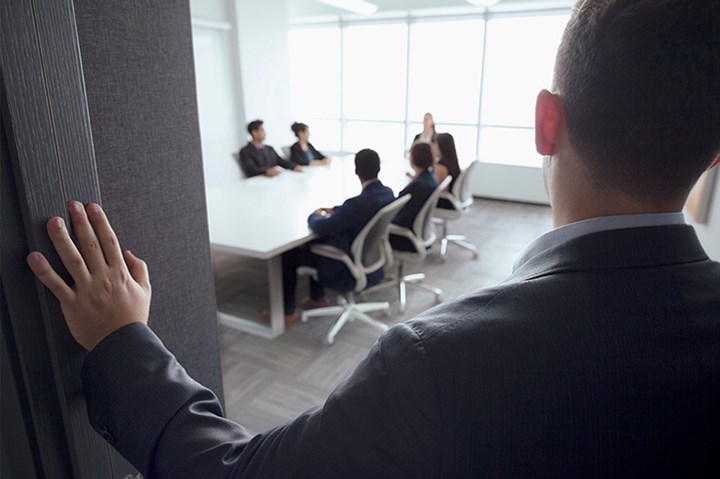
Knock-Knock: The Sustainability Auditors Are Here

Photo: Getty Images
There was a time, not so long ago, when you might have been excused for thinking that “sustainability” was mostly virtue signaling or aspirational fancy talk. But not today. It’s getting real, folks!
I interviewed a molder this week for an upcoming article, and he voiced something that a number of you may be experiencing – and others will soon, no doubt. It used to be that custom processors like this injection and blow molder had to satisfy the customer’s engineering and purchasing teams that they would get a good product at a good price and on time. But nowadays, this molder, whose business is increasingly in medical and pharmaceutical products, has another point of interaction with customers:
“They have a whole team asking sustainability questions now. Most of our machines are all-electric now, saving energy. Our paperboard boxes are 100% recycled material. We’re looking into returnable plastic totes for shipping. But they want to know more – Are we using all-LED lighting? Are we taking steps to not waste water? Are we following all the proper labor regulations?”
Yes, it’s a whole new world. One signpost to that new world is the growing focus on carbon footprints. I’ve written several times recently about how those footprints are calculated – not a task to be approached casually. There are innumerable factors to consider, but some of your suppliers are starting to make things easier by offering carbon footprints for their products, like resins, injection machines and molds.
The latest addition to this trend is an announcement by BASF that it can provide customers with carbon footprints for several of its additives – antioxidants and light stabilizers in its Irganox, Tinuvin and Chimassorb portfolios. BASF can now provide “cradle-to-gate” product carbon footprints that comprise the total greenhouse gas emissions that occur from extraction of resources to the manufacturing of the final chemical product.
You many not used stabilizers from BASF, resins from Asahi Kasei, Arburg injection machines from Arburg, or molds built by Haidlmair – so their carbon footprints won’t be precisely accurate for you. But until your particular materials, additives and equipment suppliers come up with their own carbon footprints, you could perhaps use them for an approximation to calculate your own carbon footprints.
Read: If You Like Wrestling with Carbon Footprints…
I may get some grief for that last sentence, but I’m only making a practical suggestion for a first-pass estimate of your carbon footprint. Consider, for example, the potential differences in inputs to the carbon footprint of tooling from your moldmaker versus those from Haidlmair in Austria. There’s the manufacture and transport of the raw steel; the waste “chips” cut away in CNC milling to produce your particular mold shape; the amount and source (renewable or otherwise) of electrical energy consumed in that mold’s production; further energy for mold tryout at the toolmaker, perhaps; materials for packaging the mold for transport; and the energy consumed in shipping the mold to your shop. How much those factors might differ from one moldmaker to another, and how much those differences might weigh against the overall carbon footprint, I have no idea. Ditto for the “embodied energy” in manufacturing an injection machine, which Arburg says can involve around 11,000 components.
Going back to that medical molder I interviewed a few days ago, he never mentioned that anyone had asked for his carbon footprint. But tomorrow they might. He wouldn’t find any simple answer available, but he could get some guidance from a new book I’ve reviewed elsewhere, Sustainability Management in Plastics Processing by consultant Dr. Robin Kent. That, and a whole lot of patience and perseverance and some good luck, is all he’ll need.
Leave a Reply