
Arburg Debuts Electric Injection Molding Machine for Asia
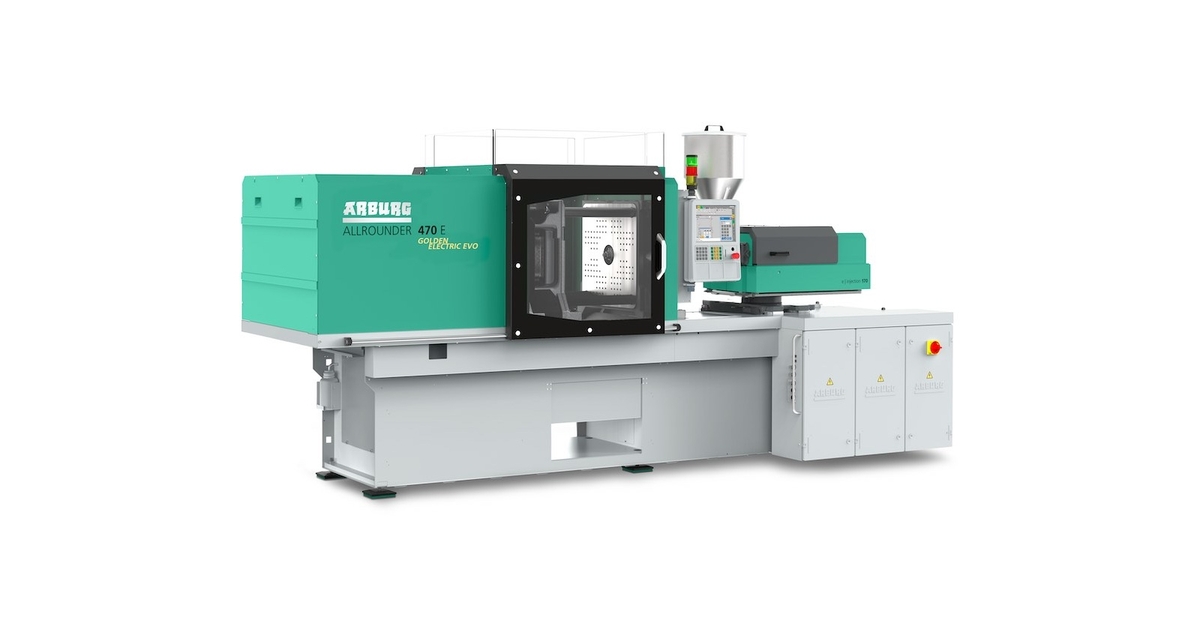
Arburg set the initial course for its “local-to-local” activities back in 2020, with the opening of the Arburg Technology Factory (ATF) in Pinghu, China, near Shanghai. Initially, activities focused on adapting Allrounder machines to customer-specific requirements and implementing turnkey systems in cooperation with local suppliers of molds and peripheral equipment. This was followed in 2023 by the Flexlift linear robotic system and now the Allrounder Golden Electric EVO. Both product series are specifically tailored to the requirements of customers in Asia, where they are exclusively marketed
Assembly in the ATF ensures quick availability of the entry-level electric machines. The portfolio includes machine designations 370, 470, 520, and 570, which cover clamping forces ranging from 600 to 2,000 kN. The injection units range from size 100 to 800 for shot weights up to around 430 grams of polystyrene (PS).
Precision, speed, and energy efficiency.
Arburg said that the Allrounder Golden Electric EVO is extremely precise, thanks to its high-quality injection units. The servo-electric drives for inject, dose, and open and close mold deliver fast acceleration, high speeds, and simultaneous movements, all of which add up to short cycle times. Dry cycle times are up to two seconds shorter than standard hydraulic machines, according to Arburg. What’s more, energy use can be reduced by up to 50% with the toggle-type clamping unit, the high efficiency of the servo-electric drive, and recovery of braking energy, said Arburg.
Just for Asia: The Flexlift robotic system.
Another product designed for the Asian market is the Flexlift, a cost-effective reliable, rapid, and precise robotic system. Its minimal height and telescopic design make it suitable for confined spaces. Powerful servo motors ensure highly dynamic and precise performance of the vertical mold-entry axes. This enables fast removal, accurate and vibration-free movements, and short cycle times.
In addition, automation and applications experts at Arburg’s ATF in Pinghu develop turnkey and tailored complete solutions in cooperation with local partners. An example exhibited at Chinaplas was for liquid silicone rubber (LSR) processing.
Heat- and media-resistant LSR components.
An electric Allrounder 470 E Golden Electric EVO with 1,000 kN of clamping force, LSR cylinder, and vacuum equipment was used to mold LSR-based valves for automotive applications at Chinaplas. The material from Wacker — Elastosil at Shore hardness 50 A — is resistant to heat and media and offers good resilience and consistently high performance. Using an eight-cavity mold from Chinese partner Gaoyuan, LSR components weighing 0.8 grams are produced in a cycle time of around 55 seconds. Injection is sprue-less and performed directly via a pneumatic cold runner system. The LSR dosing unit is supplied by Arburg partner 2KM. A Flexlift 10 linear robotic system gently removed the molded parts from the tool and placed them on a conveyor belt.
Leave a Reply