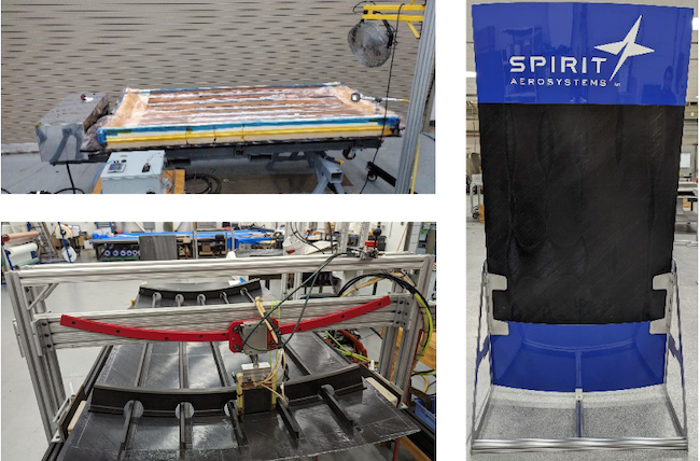
JEC Composites Innovation Awards: Finalists in Aerospace Process Category
The 2024 edition of the JEC Composites Innovation Awards has kicked off with the naming of three finalists per category. The awards ceremony will take place in Paris on Feb. 8, 2024. Here we profile the successful entries in the Aerospace Process category.
Aspera welded thermoplastic composite demonstrator
Company: Spirit AeroSystems (USA)
Partners: A&P Technology (USA), Concordia Fibers (USA), Electroimpact (USA), Mitsubishi Chemical Advanced Materials (USA), NIAR (USA), Victrex (USA)
![ASPERA1_650x428[49].png ASPERA1_650x428[49].png](https://eu-images.contentstack.com/v3/assets/blt08823f5db61ded5d/blt74688e01d7eea91c/65b2e517afc23e040ae81fdc/ASPERA1_650x428[49].png?width=700&auto=webp&quality=80&disable=upscale)
Image courtesy of Spirit AeroSystems
Description: In preparation for future aerospace challenges, Spirit AeroSystems has fabricated details utilizing automated fiber placement, stamp forming, and novel pressure intensification processes. Welding is done with the patented Co-Fusion and induction processes, demonstrating fastener-free high-rate manufacturing. Aspera is representative of a large portion of a typical commercial aircraft cabin but is made entirely from thermoplastic composite details welded together.
Fastener-free assembly methods are adopted to minimize weight and cost while utilizing rapid fabrication processes that enable future high-rate single-aisle commercial aircraft production. Both patented and proprietary novel fabrication and welding processes are used to make the part. These processes were developed internally by Spirit AeroSystems and represent state-of-the-art thermoplastic composite technologies and tooling methodologies.
Key benefits
-
Rapid fabrication process cycle time, with a dramatic reduction in energy consumption
-
Elimination of fasteners and associated scrap, rework, and weight
-
Materials used can be reworked in process and recycled at end of life
-
Efficient combination of welding and consolidation cycles with patented process
-
Development of rapid in-situ induction welding process with minimal unused heat energy
EmpowerAX – additive functionalization
Company: German Aerospace Center
Partners: 9T Labs AG (Switzerland), Airtech Europe (Luxembourg), Ansys Switzerland GmbH (Switzerland), CEAD B.V. (Netherlands), Ensinger GmbH (Germany), Fiberthree GmbH (Germany), Fill GmbH. (Austria), Hans Weber Maschinenfabrik GmbH/Weber Additive (Germany), Prime Aerostructures GmbH (Austria), Siemens AG (Germany), Suprem SA (Switzerland), SWMS Systemtechnik (Germany)
![EmpowerAXDemo650x461[58].jpeg EmpowerAXDemo650x461[58].jpeg](https://eu-images.contentstack.com/v3/assets/blt08823f5db61ded5d/blt7fb7a45d0bf459c9/65b2e623ebbcff040aa34fcb/EmpowerAXDemo650x461[58].jpeg?width=700&auto=webp&quality=80&disable=upscale)
Image courtesy of German Aerospace Center
Description: The EmpowerAX demo part is a multi-curved thermoset shell additively functionalized with short and continuous fiber-reinforced elements realized by the DLR Innovation Lab and 12 EmpowerAX members. It demonstrates the industrially available process chain for additive functionalization. Cost-efficient composite manufacturing is combined with the agility and design freedom of additive manufacturing.
Key benefits
-
Cost-efficient composite manufacturing
-
Overprinting of a multi-curved shell
-
Combines thermoset and thermoplastic polymers
-
Short and continuous fiber-reinforced materials
-
Industrially available process chain
One-shot in situ consolidation wing upper cover
Company: Airbus DS – Defence & Space (Spain)
Partner: FIDAMC (Spain)
![Airbus_DS2_650x228[26].png Airbus_DS2_650x228[26].png](https://eu-images.contentstack.com/v3/assets/blt08823f5db61ded5d/blt358d179942d5f160/65b2e68331e2ca040a3438bd/Airbus_DS2_650x228[26].png?width=700&auto=webp&quality=80&disable=upscale)
Image courtesy of Airbus DS
Description: One-step in situ consolidation of polyetheretherketone (PEEK) thermoplastic resin based carbon-fiber composite was used to fabricate a transport aircraft external wing skin cover, which is part of the primary structure, through an ecofriendly process. This approach enables low energy consumption processing and end-of-life recycling.
Thermoplastic resin based composites are a key enabler toward sustainability of composite structures in aerospace due to their recyclability and performance. Airbus Defence and Space (engineering) and FIDAMC (manufacturing) have produced a thermoplastic in-situ consolidated (ISC) upper cover for airframe under the ITD CleanSky2 platform for integration into an outer external wing box specimen. This is the first demonstrator of a primary structure using ISC with integrated stringers and without a post-consolidation step. An exhaustive testing campaign substantiated technology readiness level (TRL) 5, including mechanical characterization, detail, subcomponent level, and full scale up to ultimate load.
Key benefits
-
Weight performance through structural integration in one-shot consolidation
-
Improved recyclability
-
Automation
-
Eco-efficient processing
-
Promising new repair technology via welding
Leave a Reply