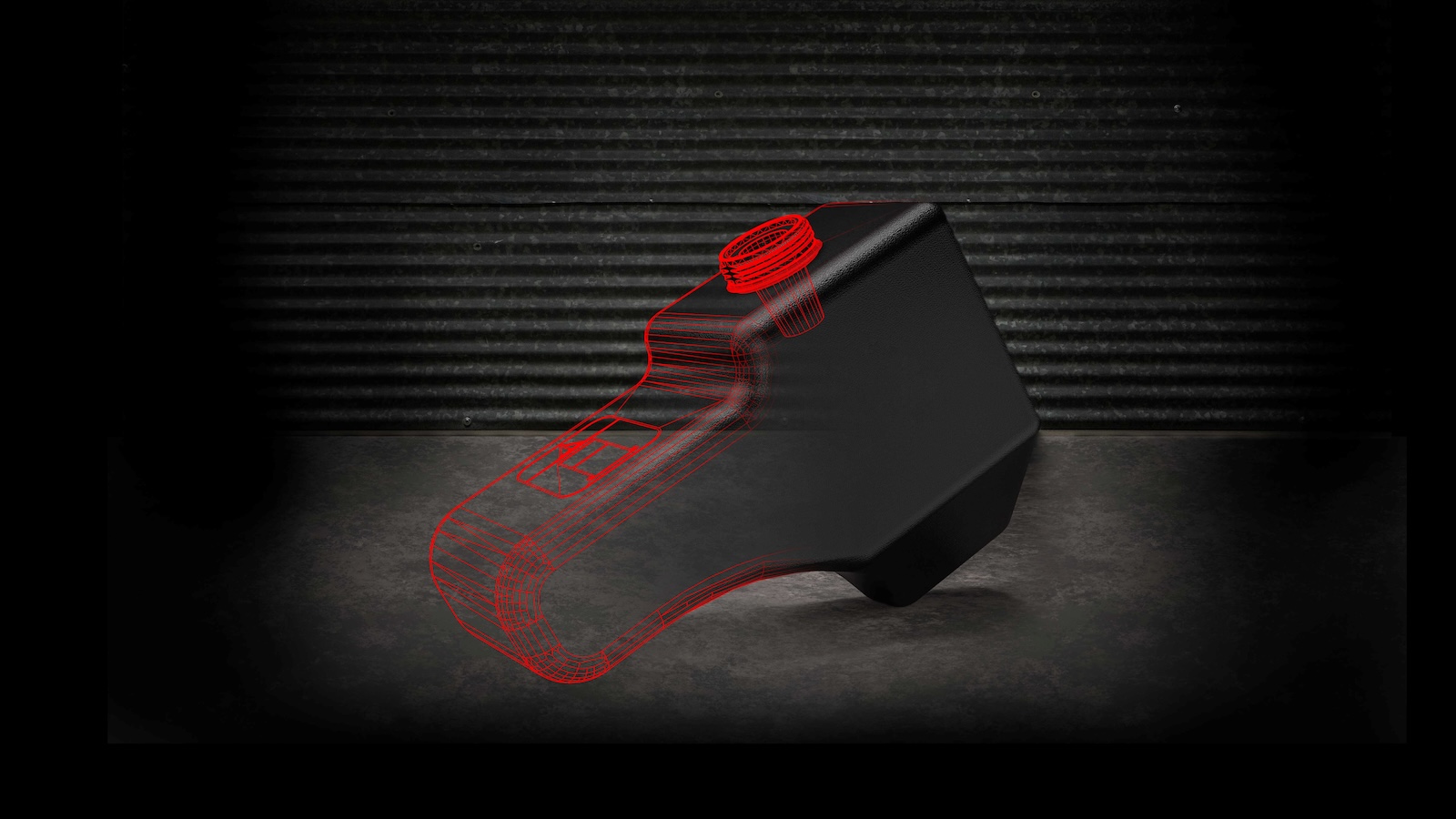
Rotomolded Acetal Fuel Tanks Viable Alternatives to Fluorinated HDPE Tanks
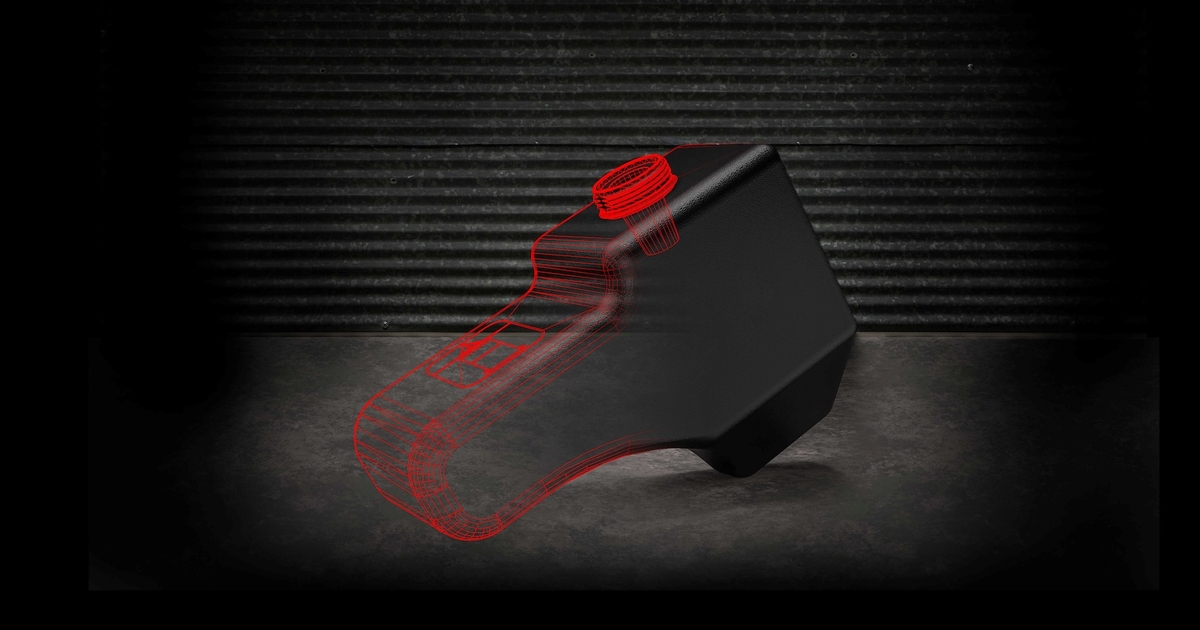
Rotomolded fuel tanks made of acetal, produced via Gemstar Manufacturing’s Robomold robotic rotomolding technology, have been identified as a highly viable alternative to fluorinated fuel tanks in the wake of an Environmental Protection Agency (EPA) decision to halt the production of fluorinated coatings for high-density polyethylene (HDPE) containers due to per- and polyfluoroalkyl substance (PFAS) contamination.
Gemstar has commercialized several EPA-certified acetal fuel tanks made with its unique Robomold robotic rotomolding process as a fluorination-free solution. “Our innovative technology is a highly viable option that can fill the emerging needs of OEMs and molders who are struggling to fill production needs amidst disrupted supply chains,” said Kevin Lumberg, channel manager for Gemstar Manufacturing.
Monolayer technology enables design flexibility
Gemstar’s exclusive Robomold technology reportedly provides tighter tolerance control with precision-distributed heat and material control for consistent part repeatability and optimized strength-to-weight ratios. It is also said to allow for unsurpassed design flexibility, including the ability to layer different compounds and coatings into finished parts. Rotomolded acetal fuel tanks provide single-layer barrier protection that meets EPA requirements in comparison to injection-molded HDPE tanks that require fluorination.
Polyamide (PA) 6 has historically been the only material option to achieve a permeation barrier with a single-layer rotomolding process. However, PA 6 is difficult to rotomold and yields a high scrap rate and poor cosmetic appearance. In comparison, acetal delivers a single-layer structure that achieves permeation requirements and provides good processability, low scrap rates, and favorable cosmetics.
Acetal has previously been used in injection-molded fuel tanks, but material suppliers have now developed new rotomolding grades that incorporate additive packages that raise the heat performance.
Multiple heating and cooling zones
Robomold’s computer-controlled technology allows for precise control of multiple heating and cooling zones, customized material flow, optimized material use, increased product quality, and part traceability. It also offers instant cycle data collection, reduced cycle times, focused cycles for highly engineered resins, and the elimination of labor-intensive processes.
The core of the technology is a six-axis robot that delivers a greater degree of rotation than traditional rotational molding. Instead of using a heating oven, the robot tumbles the electrically heated mold, which incorporates a multitude of separate heating zones. Direct heat applied to these zones enables resin to reach its ideal processing temperature and permits manufacturers to create geometries that were previously unattainable.
Less scrap, more sustainability
Robomold also delivers a range of sustainability advantages compared to conventional rotational molding. Robotic rotational molding reduces cycle times by 25 to 30% with little to no scrap compared to traditional rotomolding. Researchers at Queens University Belfast recently reported that Robomold’s electrical mold heating method takes significantly less time to heat the mold compared with a conventional oven, saving more than nine minutes (22%) with no appreciable difference in part quality.
As end-use requirements become more stringent, Robomold robotic rotational molding is also finding greater use in custom applications. It is reportedly ideal for military, OEM, industrial, and commercial applications, where precision and unsurpassed repeatability are required.
Leave a Reply